Understand the applicable environment, temperature, pressure and other physical parameters of alloy steel pipe products to ensure that they meet specific needs. Choose the products of large enterprises and brand manufacturers to ensure quality and after-sales service.
Check the product quality certificate issued by the alloy steel pipe manufacturer and the certificate number of the implementation of production license management to ensure that the product is legal and compliant.
Check the surface quality and marking of alloy steel pipes, including grade marks, standards and diameters. If there are cracks, scars and other defects, need to be measured and detected by the instrument.
Pay attention to observe whether the surface of the alloy steel pipe cracks, scars and other defects, if necessary, through the instrument to measure and detect. Continuous technical updates are made during the production process to improve product quality.
The technical requirements of superalloy steel tubes for cracking furnaces are introduced, including the process of molecular chain fracture of hydrocarbons into small molecular weight unsaturated hydrocarbons at high temperatures (above 700°C). High temperature resistant in the pyrolysis process, accompanied by condensation, cyclization and dehydrogenation reactions. The basic factors affecting cracking are first temperature and duration of reaction, as well as the type of hydrocarbon raw material. The process of thermal cracking in chemical production, in a cracking furnace (tubular furnace or regenerative furnace), to change petroleum hydrocarbons into small molecules of alkenes, alkynes, and aromatic hydrocarbons, such as ethylene, propylene, butadiene, acetylene, benzene, and toluene.
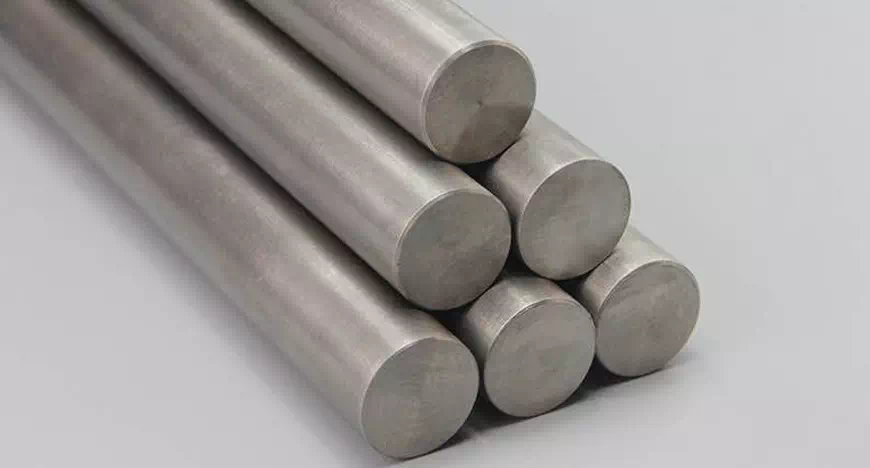
Welding technology of alloy steel pipe:
a. Welding wire using HSCuNi material welding wire must be stored in a dry, well-ventilated warehouse, strictly protected from moisture.
b. Primary pure argon is used as the protective gas.
c. Tungsten argon arc welding, tungsten using cerium tungsten electrode.
d. Using DC argon tungsten arc welding machine, the diameter of the electrode depends on the welding current.
e. Welders must be trained in B10 pipe welding and qualified before welding.
f. The machining of the welding groove must be carried out by mechanical machining method.
g. For the butt welding of the pipe wall thickness not greater than 2mm, the groove can not be opened but 1.5 ~ 2mm should be left; Bevelling is required for butt welding with pipe wall thickness greater than 2mm. Groove type and size shall meet the requirements of process evaluation.
h. Before welding, both sides of the weld should be cleaned with a stainless steel wire brush or scraper within 20mm until the metallic luster is exposed.
i. For pipes and welding wires that are not seriously greasy, they can be scrubbed directly with clean cotton yarn dipped in acetone.
j. When positioning welding, welding should be performed under the same conditions as formal welding. If there is a crack in the positioning weld, the positioning weld should be removed and re-translocation the positioning weld prior to welding. The solder joint length of positioning welding is 10 ~ 15mm, and the number of points is determined according to the pipe specifications, which should be as little as possible but not less than three points.
k. Gas protection of the weld: reliable gas protection must be carried out under and on the opposite side of the weld. Front protection shall be provided by welding torch suitable for copper alloy welding or additional tailing protection. The back protection can be based on the shape and size of the weldment, using the back protection gas cover or the inner cavity of the weldment filled with argon protection.
Comments